Welding plays a critical role in the manufacturing sector, serving as the backbone for creating strong, durable products. However, as industries evolve and demands become more complex, the need for customized welding solutions is more prominent than ever. Traditional welding techniques often fall short when it comes to addressing unique challenges posed by modern manufacturing processes. This blog explores various custom welding solutions, focusing on how they can help tackle specific needs while enhancing efficiency and product quality.
Understanding Custom Welding Solutions
Custom welding solutions are tailored to meet the distinct requirements of individual projects or industries. These solutions are developed after analyzing the specific challenges faced by a manufacturer, including material types, thicknesses, and production environments. By implementing bespoke techniques, manufacturers can optimize their welding processes to improve quality, reduce costs, and increase throughput. Companies can gain a competitive edge by addressing unique challenges with custom solutions that traditional methods might not effectively resolve.
Benefits of Custom Welding Solutions
Implementing custom welding solutions offers numerous benefits that can significantly enhance a manufacturer’s operations. These solutions enable companies to achieve higher precision and consistency in their welds, resulting in improved product integrity. By customizing the welding process to fit specific requirements, businesses can also reduce the likelihood of defects and rework, saving time and resources. Furthermore, tailored welding approaches can facilitate more efficient use of materials, minimizing waste and lowering overall production costs.
Advanced Techniques for Enhanced Efficiency
Several advanced welding techniques have emerged that allow manufacturers to achieve superior results. Among these is the integration of automation in welding processes. Automated welding systems can increase speed and consistency while reducing labor costs. Robotic welding arms, for instance, can operate continuously and maintain high precision, even in complex geometries. By employing automated solutions, manufacturers can enhance their productivity and scale their operations while ensuring high-quality results.
Laser Welding: Precision and Versatility
Laser welding is a cutting-edge technique known for its precision and versatility, making it an excellent option for custom applications. This process utilizes focused laser beams to join materials, allowing for minimal heat input and reduced distortion. With its ability to weld thin materials and complex geometries, laser welding is increasingly popular in industries such as automotive, aerospace, and electronics. You can also learn more here about the advancements in laser technology and how they can be integrated into your manufacturing processes.
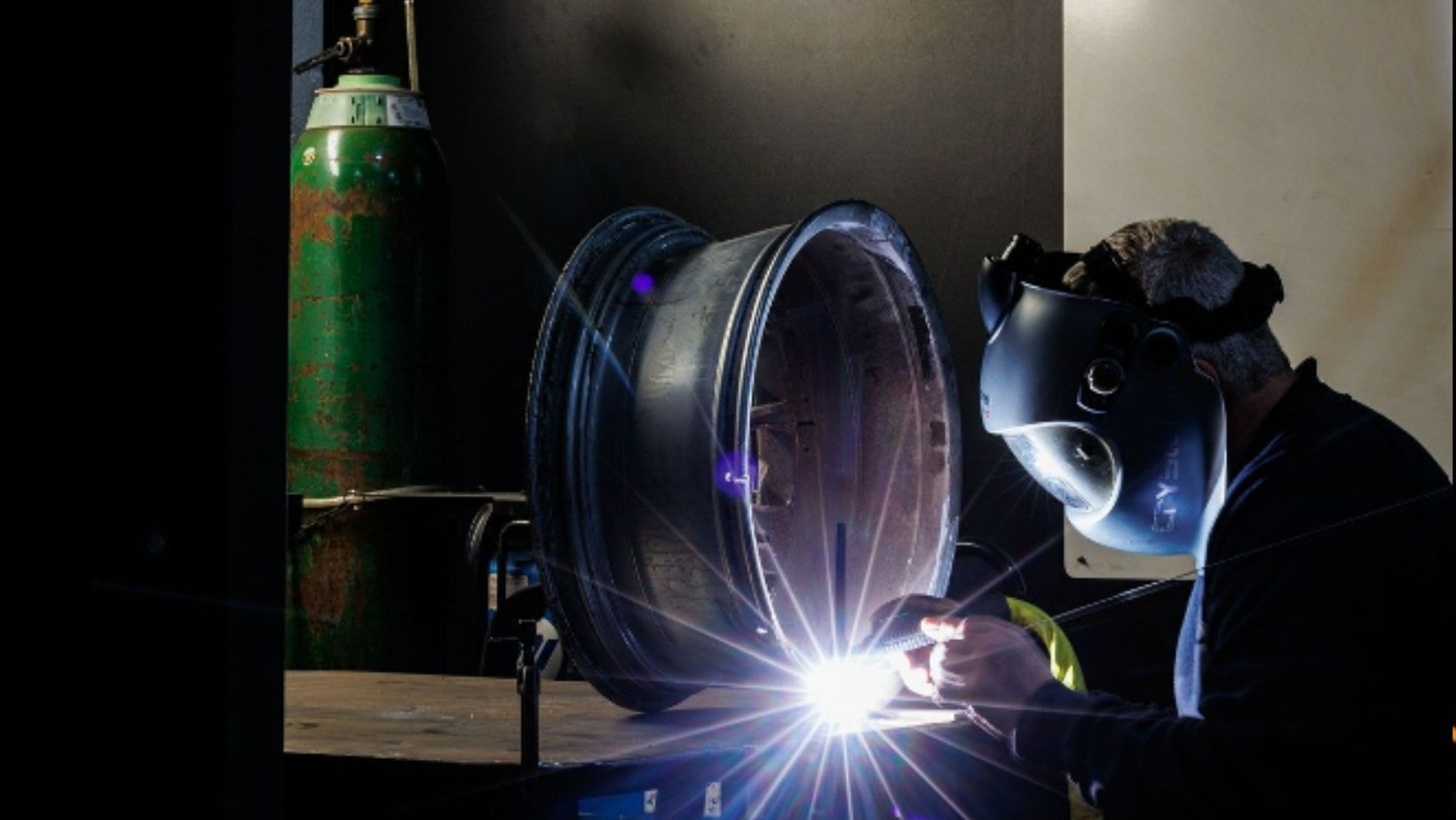
Furthermore, laser welding can be easily automated, further enhancing productivity and consistency while providing manufacturers with a significant advantage over traditional methods.
Material Considerations in Custom Welding
Selecting the right materials for a custom welding project is crucial for achieving optimal results. Different materials require different welding techniques and settings, which is why understanding their properties is vital. For instance, stainless steel, aluminum, and carbon steel each have unique characteristics that influence how they should be welded. Custom welding solutions can include specialized filler materials and processes tailored to the specific material being used. By taking the time to assess material requirements, manufacturers can enhance the strength and durability of their welded joints, ultimately leading to a better product.
Meeting Industry Regulations and Standards
Adhering to industry regulations and standards is another critical aspect of custom welding solutions. Various sectors, including aerospace, automotive, and construction, have strict guidelines governing the quality and safety of welded components. Custom welding approaches can be designed to ensure compliance with these standards, incorporating quality control measures and inspection protocols throughout the welding process.
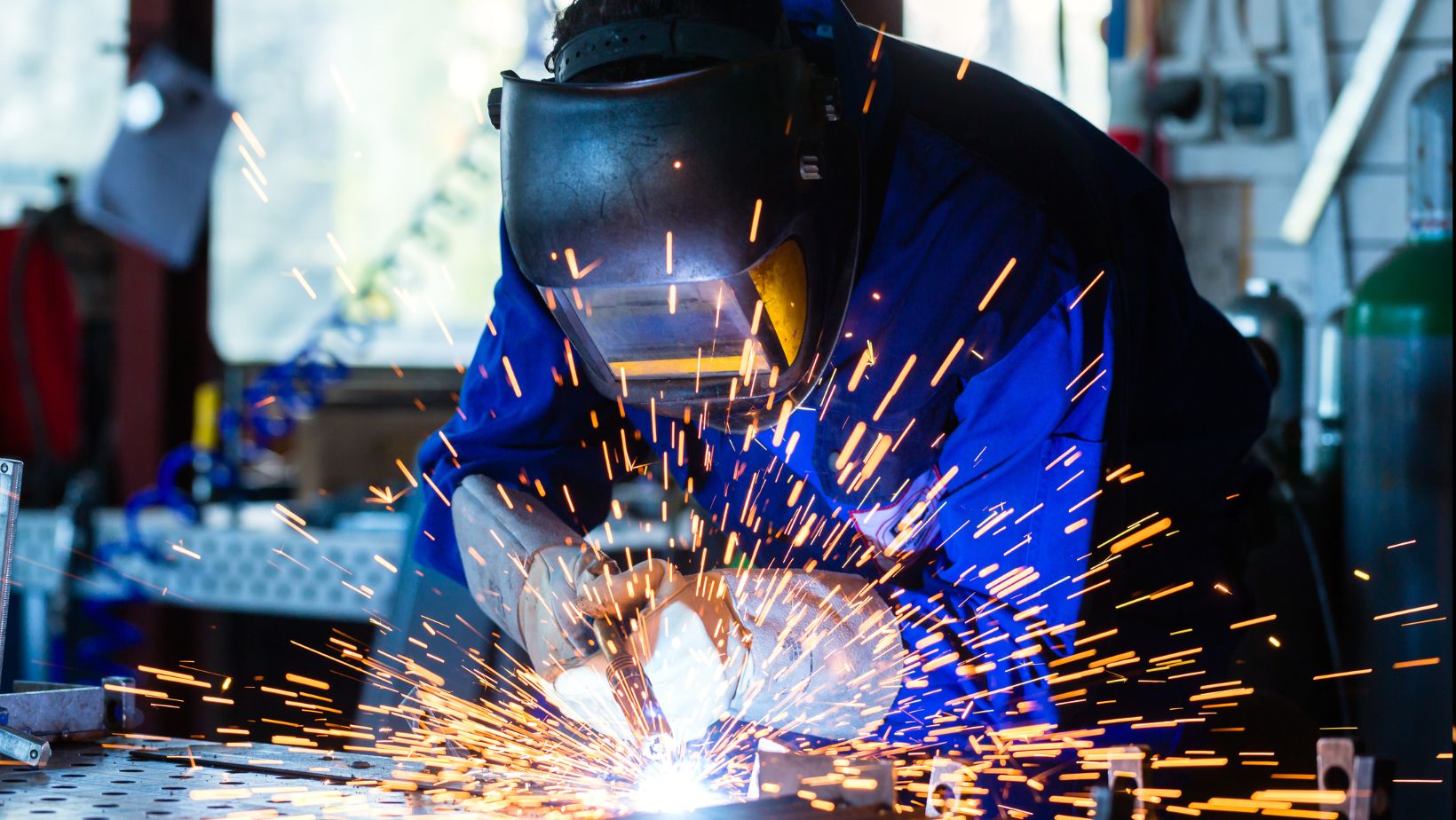
By focusing on regulatory requirements, manufacturers can not only avoid costly penalties but also build a reputation for quality and reliability in their respective industries.
The Future of Custom Welding Solutions
Page source: https://pixabay.com/photos/welding-wheel-repair-metalworking-8445458/
As technology advances, the future of custom welding solutions looks promising. Innovations in materials, equipment, and techniques will continue to drive improvements in welding processes. The rise of Industry 4.0 and smart manufacturing will further integrate welding solutions into broader production systems, allowing for real-time monitoring and adjustments. This evolution will enable manufacturers to respond quickly to changing market demands while maintaining high-quality standards. Staying ahead of the curve will be essential for businesses looking to leverage custom welding solutions to address their unique challenges.
Custom welding solutions offer manufacturers the opportunity to enhance their operations and address specific challenges effectively. By understanding the benefits of tailored approaches, advanced techniques, and material considerations, businesses can optimize their welding processes for better quality and efficiency. With the future of welding driven by technological advancements, investing in custom solutions will ensure manufacturers remain competitive and capable of meeting evolving industry demands. Embracing these innovations will pave the way for success, ultimately leading to stronger products and a more resilient manufacturing sector.